What does the automated warehouse of the future look like?
What does the automated warehouse of the future look like?
Where should you start when looking to embrace automated warehousing, and what are the challenges you might face along the way?
An automated warehouse is a breath-taking sight: picture a circuit board of activity as scores of box-shaped robots soar between pallets, scanning shelves and retrieving stock for delivery to a picking station. This is just one of a variation of scenes depicting the applications of automated technology across the UK’s warehouses.
Automation itself is not new to warehousing operations or the wider supply chain, but with recent advancements in big data and the Internet of Things, it is reaching new levels of sophistication. For businesses open to researching or developing robotic warehousing solutions, this means new opportunities to reduce labour costs, increase sorting capacity, and minimise human error.
But where should you start when looking to embrace automated warehousing, and what are the challenges you might face along the way?
Realising the scope of potential in automated warehousing
The most apparent reason for using robotics over any other form of warehouse automation is cost. When properly implemented, it reduces the amount of labour required by warehouse operations, enables higher productivity, and creates the potential to better utilise building space.
Looking more closely, many enterprises identify opportunities as a result of warehouse efficiency analysis. Robotic applications can provide greater agility and responsiveness when integrated with smart data and integrated systems.
Take critical cut off times for example: a warehouse might receive an order at 18:00 and need to ship it by 18:30. It is essential that this order can be rapidly processed or it will not ship on time. This can have repercussions as far reaching as the end customer, impacting service levels.
Another trigger, which many enterprises often overlook when considering the applications of robotics, is health and safety. Warehouses are typically hazardous environments, requiring businesses go to great lengths to ensure operators are kept out of harm’s way. Automated solutions can augment the human element in certain tasks, removing health and safety risks and limitations completely. A great example of this is a stock take. By using a small drone with a camera, you can easily go into the air and inspect a pallet stored 12m high. No more safety harnesses. No more special lifts. No more risk.
How do robotic solutions actually integrate into a warehouse?
Within warehousing, robotics solutions can be split into several areas. You have robotics for storage purposes, which includes all types of cranes or so-called automated storage and retrieval systems (ASRS).
A forklift vehicle would struggle to reach pallets stored 16m from the ground for example, so an automated retrieval system gives a better utilisation of height. And because the robotics system can be incredibly precise, the retrieval process takes less time per operation.
Outside of this fully automated perimeter, any warehouse vehicle can become an automated guided vehicle (AGV) by installing a robotic module. The benefit is these machines work in existing warehouse installations, meaning they can be introduced relatively quickly and don’t require a complete overhaul of existing processes.
What new challenges does robotic warehousing introduce?
One of the potential downsides is that robotics are much more sensitive to tolerances. By definition, an automated vehicle is set to follow pre-programmed instructions. A human can deal very easily with an uneven floor, for example. For an AGV, this could cause a significant problem.
Imagine you’re managing a warehouse and you’re receiving pallets from your suppliers. If the pallet is loading inside a fully automated system or handled by any form of AGV, it needs to be within certain criteria. The wooden pallet itself should be in good condition, there shouldn’t be any nails protruding from it, and its contents should be secured.
Manually, these issues can be managed on a case-by-case basis as people identify, react and adapt to situations. Using robots, they can be critical failure factors. You could find yourself in a situation where you need to carry out a great deal of work to bring the pallets up to the quality standards required by the automated system or to be able to present them to AGVs.
Businesses can either manage this process with suppliers, which can be tricky, or put in extra labour to do this rework, which will cancel the benefits in terms of labour savings from the AGVs.
How are businesses already preparing for the future of warehousing?
The potential savings made possible by robotic warehousing are huge, especially at enterprise level, but it is important to realise there are hidden details that should be sorted out before a business even gets to a trial stage. If you introduce AGVs before you have identified the challenges unique to your supply chain, and then encounter an issue you can’t easily overcome, you will have to postpone the launch while you reinvest into working it out. Preparation through mapping, simulation and process trials is vital. Many companies are exploring these options because they promise an increase in warehouse efficiency that translates into direct savings.
But we’re not just talking about warehouse efficiency measures; robotics also promises a level of supply chain agility that either cannot be achieved today or is very costly. Think about robotics as essentially free, through-the-night labour. This makes it incredibly appealing, especially to enterprises with escalating distribution costs due to the need to react quickly to customer orders or variance in demand.
Integrating robots picking, packing and handling products with an online ordering system, a ‘chatbot’ for customer support and the appropriate level of analytics to manage across a complex supply chain is the dream of many FMCG companies. But developing these integrated systems requires careful detailed analysis of the entire supply chain and demand cycle.
Robots moving pallets are the thin end of the wedge when it comes to the benefits that can be delivered by integrating automation into a truly intelligent, agile supply chain. Surfacing the potential issues and achievable benefits with supply chain experts who can plan the end-to-end system is the essential step in getting your supply chain ready for robots.
Source: www.themanufacturer.com
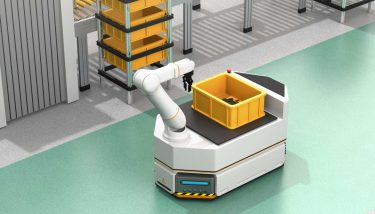
Self driving AGV (Automatic guided vehicle) with robotic arm moving beside conveyor